Electronic Products & Appliances
Shock & Impact Protection Solutions
Shock and impact protection are essential for safeguarding the internal components of electronic products and appliances against potential damage resulting from impacts or accidental drops. At Armstrong, our expertise in die-cutting, thermoforming, and elastomer molding enables us to create customized solutions that effectively dissipate impact energy, thus minimizing the risk of damage.
Devices
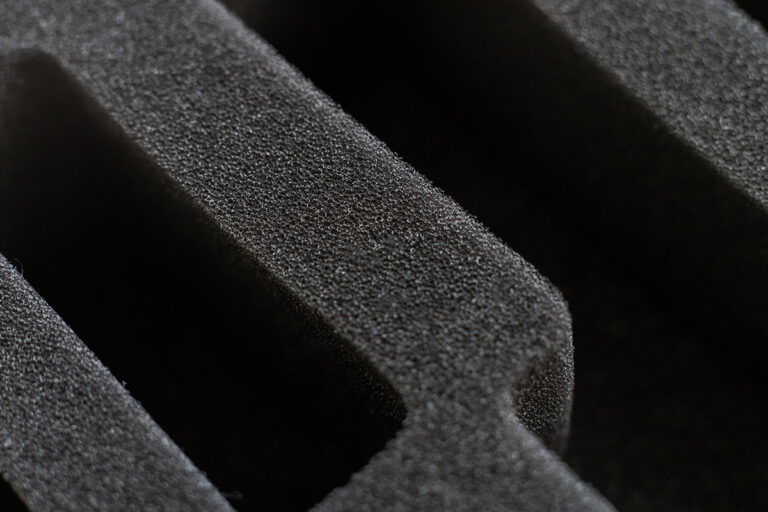
Inserts and inlays
Requirements
- Must be precisely tailored to the dimensions and shape of the items and the interior of the protective case
- Excellent shock-absorbing properties to protect the items from impacts or drops, while minimizing the risk of scratches or other forms of physical harm.
- Durable for repeated use with ability to resist deformation, tearing, or breaking down under normal handling and transportation conditions.
- May require static discharge protection or resistance to moisture depending on requirements
Solutions
- Process: Die cut; Materials: PE foam, EVA foam, PU foam
- Process: Heat press forming; Materials: PE foam, EVA foam
- Process: Vacuum forming; Materials: PE foam, Plastic films (HIPS, HDPE, PP)
Dunnage
Requirements
- To protect and secure items during handling in manufacturing, transportation or storage
- Capable of absorbing shocks and impacts, preventing damage from vibration, and minimizing the risk of scratches or other forms of physical harm.
- Durable for repeated use with ability to resist deformation, tearing, or breaking down under normal handling and transportation conditions.
- May require static discharge protection or resistance to moisture depending on requirements
Solutions
- Process: Die cut; Materials: PE foam, EVA foam, PU foam
- Process: Vacuum forming; Materials: PE foam, Plastic films (HIPS, HDPE, PP)
Electronic Parts & Components
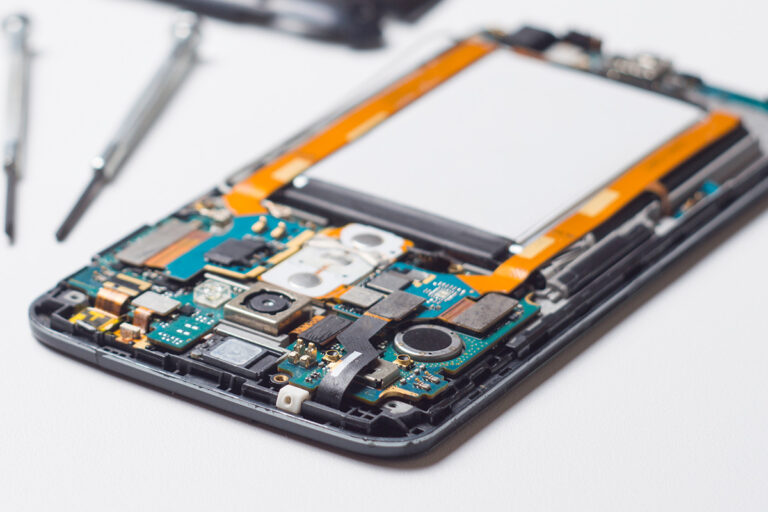
Electronic Parts & Components
Requirements
- Must be firm enough to hold component in place and compressible enough to withstand dimensional changes over the life during operation of the component
- Reliable compression set resistance (C-set) and stress relaxation performance over a broad range of operating conditions
- Able to absorb the impact energy as required
Solutions
- Process: Die cut; Materials: Microcellular PU foam, PE foam, PP foam