Medical Devices
Solutions for Medical Devices
At Armstrong, we understand the utmost importance of safety, cleanliness, and biocompatibility in manufacturing of medical devices. You can rely on us to deliver high-quality custom foam, film and elastomer solutions for medical devices that meet the strict requirements of the medical and healthcare industry.
Patient Comfort & Support Solutions
At Armstrong, we pride ourselves on our extensive network of industry partners and our access to a wide range of high-quality materials specific for medical devices. This, coupled with our expertise in manufacturing processes and techniques, enables us to provide superior solutions that prioritize optimal patient comfort and satisfaction.
Padding, Cushioning & Lining

Polyurethane (PU) foam
Light weight, open-cell foams with excellent resiliency, chemical resistance & hygroscopicity, and when heated to suitable temperatures, are moldable. Retains its form stability and returns to its original or close to original shape, even after permanent load. Breathable and wicks moisture away from the skin. Excellent for cushioning.
Applications
- Positioning devices
- Pressure relief devices
- Fixation devices
- Cushioning for wheelchair, surgical helmets and headrests
Methods of Manufacturing
- Die-cut, Thermoforming, Reaction Injection Molding, Lamination and Coating
Micro-cellur Polyurethane (PU) foam
PU foams with dense, open-cell, thermosetting structures that are non-heat moldable. Stable in form, elastic, shock-absorbing, odorless, and washable. Provides one of the highest degrees of shock absorption. Retains its form stability and returns to its original or close to original shape, even after permanent load. Breathable and wicks moisture away from the skin.
Applications
- Orthotic & prosthetic arch support and high impact applications
- Positioning devices
- Pressure relief devices
Methods of Manufacturing
- Die-cut, Thermoforming, Reaction Injection Molding, Lamination and Coating
Polyethylene (PE) foam
Closed-cell foams that are nontoxic, resistant to chemicals and fluids, lightweight, strong and durable with excellent shock absorption and moisture resistance. When heated to suitable temperatures, they are moldable. Tendency to permanently compress or “bottom out” over time under load. Readily washable and discourage bacteria growth.
Applications
- Total-contact orthoses
- Prosthetic liners
- Wheelchair seating systems
- Compression garments
Methods of Manufacturing
- Die-cut, Thermoforming, Reaction Injection Molding, Lamination and Coating
Ethyl Vinyl Acetate (EVA) foam
Foams with closed-cell co-polymer (ethylene and vinyl acetate) structures that are similar to PE foam however softer, more resilient and elastic. Have slightly higher compression set compared to PE foams and may take longer to fully recover after being compressed.
Applications
- Insoles, top and bottom covers, wedges, cushioning material, and shell material for accommodative and functional orthoses
Methods of Manufacturing
- Die-cut, Thermoforming, Reaction Injection Molding, Lamination and Coating
Medical Device Components
At Armstrong, we recognize the utmost significance of safety and effectiveness in medical devices. Our full commitment to ISO 13485 standards ensures that our solutions not only meet regulatory requirements but also exceed the expectations of our valued customers.
Device Parts & Components
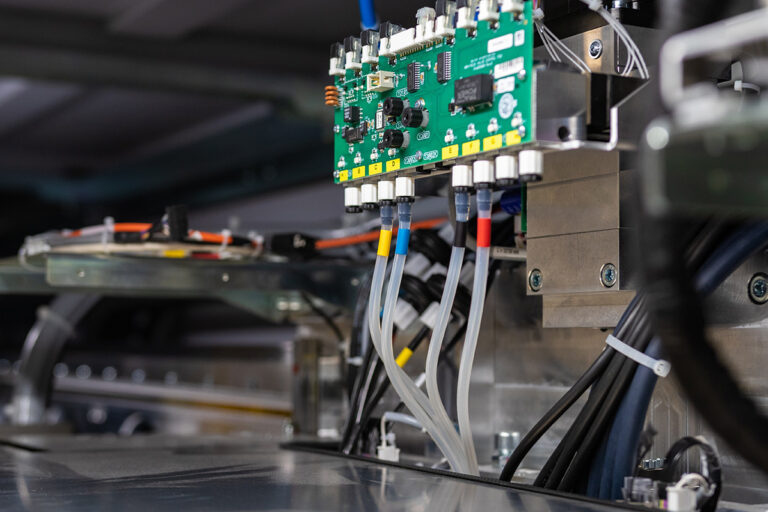
Seals & Gaskets
Applications
- A1: Gasket for syringes & IV injection site sets
- A2: Bioreactor seals, autoclaves seals
- A3: Sealing/ gasket in fluid handling system
Materials
- For A1: IR rubber
- For A2: EPDM rubber
- For A3: FKM rubber
Methods of Manufacturing
- Elastomer moulding
Pulleys, wheels, bushing & rollers
Applications
- Medical Devices & equipment
Materials
- Urethane rubber
Methods of Manufacturing
- Elastomer moulding
Thermal Management
Applications
- Medical wearables, electronic devices & equipment
Materials
- Thermal interface gap pads, phase change materials, graphite sheets, thermal adhesives
Methods of Manufacturing
- Die-cut
Electrical insulations
Applications
- Medical wearables, electronic devices & equipment
Materials
- PVC film, Polyimide film, PET film, Vulcanized fiber
Methods of Manufacturing
- Die-cut
Grommets, boots & sleeves
Applications
- A1: Tubing, probes, valves, infusion pump, ventilators, surgical instruments
- A2: Diagnostic devices
- A3: Cables & Wires
Materials
- For A1: Silicone rubber
- For A2: EPDM rubber, FKM rubber, NBR rubber, Silicone rubber
- For A3: EPDM rubber, FKM rubber, NBR rubber, CR Rubber, Silicone rubber
Methods of Manufacturing
- Elastomer moulding
Diaphragms
Applications
- Pressure regulators, pumps, and control valves, Inhalers and Respiratory Devices
Materials
- Silicone rubber
Methods of Manufacturing
- Elastomer moulding
Cushions & Pads
Applications
- Orthopedic braces & supports, Prosthetic devices, wheelchairs & mobility aids, positioning devices, hearing aid, face masks & respiratory devices, rehabilitation & assistive devices
Materials
- M1: PE foam, EVA foam, Microcellular PU foam, PU foam, PP foam
- M2: PU
Methods of Manufacturing
- For M1: Die-cut
- For M2: Reaction Injection Moulding
Grips & Handles
Applications
- Surgical instruments, hand-held diagnostic devices, and rehabilitation equipment
Materials
- Silicone rubber
Methods of Manufacturing
- Elastomer moulding
Electronic component compression pads & cushions
Applications
- Medical wearables, electronic devices & equipment
Materials
- Microcelluar PU foam, PE foam, PP foam
Methods of Manufacturing
- Die-cut
Membrane Keypad
Armstrong’s membrane keypads are meticulously engineered to excel in the challenging healthcare environment, offering exceptional durability, effortless maintenance, and effortless cleaning. With our customizable options, you can seamlessly integrate our keypads into your device.
Medical devices & equipment interfaces
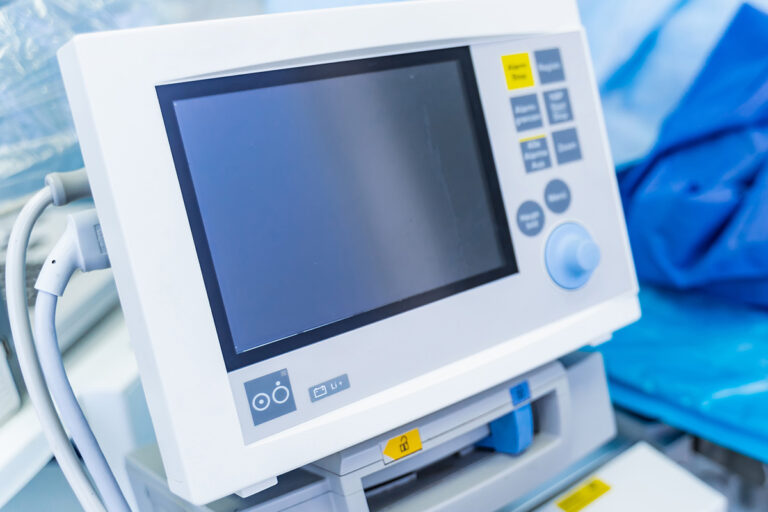
Customization options available
- Graphic Overlays: Options include transparent and tinted display windows, textures and UV hard-coat surface finishes, and pillow embossed keys or a cosmetic rim emboss on the graphic overlay.
- Backlighting: Options include Light Guide Film (LGF), Light Emitting Diodes (LED), Electroluminescent (EL) Lighting and Fiber Optic Lighting.
- Button Response: Options if key actuation requires a tactile response include stainless steel domes, embossed polyester domes or tactile embossed graphics.
- Circuits: Various options for substrates, connectors and circuit protections. Substrates: Printed Circuit Board (PCB) or Flexible Printed Circuit (FPC). Connectors: Male connector, female connector, soldered, or ZIF. Circuit Protection: ESD, EMI, and RFI protection can be integrated into the circuit
- Back / Support Panels: Available in a variety of materials to suit your application.
Next-Gen NVHM Solutions for a Smarter, Safer & Greener Future
At Armstrong, we understand the changes and challenges of the Noise, Vibration, Heat & Safety landscape of today’s world, and we’re committed to provide solutions to meet this growing critical need. We’re passionate about what we do and are dedicated to help make the world a more pleasant place to live in.

Receive an accurate quote within 3-5 days when you fill out this form. Or, give us a call: +65 6804 9623