Foam Thermoforming
Shaping Your Ideas Into Reality With Thermoforming
For more than a decade, Armstrong has been providing customers with unique and innovative thermoformed foam solutions. With our combined custom design services with specialized production capabilities, we can provide solutions that are able to meet your most complex product needs. We also provide comprehensive support services throughout the production process to ensure quality standards and cost efficiencies are met. If you’re looking for a partner that you can trust to provide the best possible solutions, then Armstrong is the right choice for you.
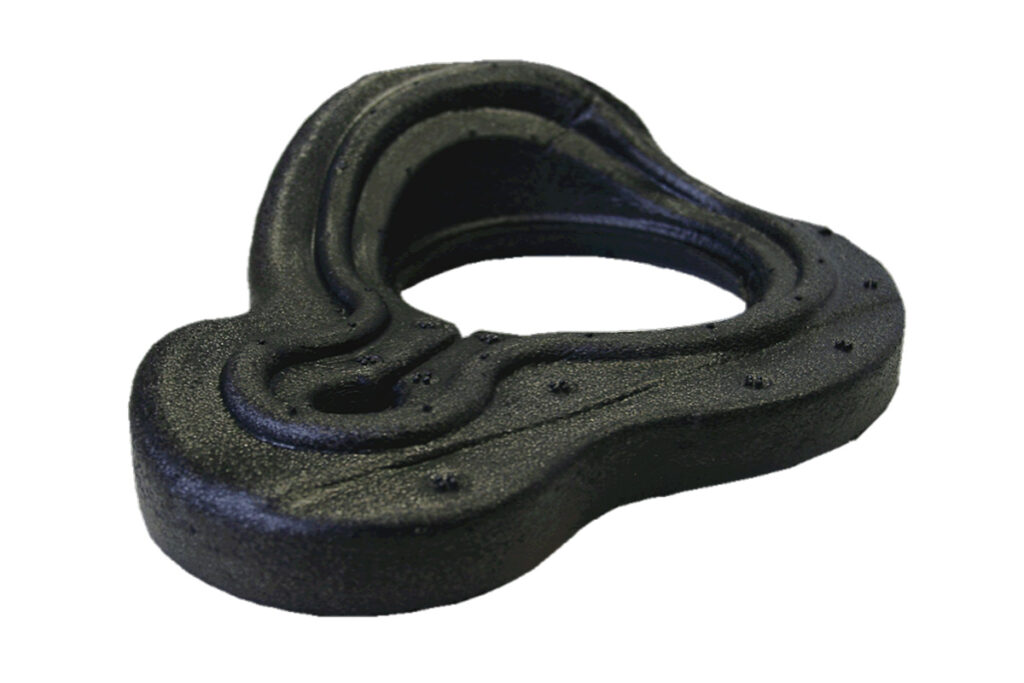
Our Capabilities
Our foam thermoforming process capabilities include heat process forming, vacuum forming and twin-sheet thermoforming. Each process provides formed parts with unique characteristics.
Heat Press Forming
Material is pressed by male & female mold via pressure & temperature
- Features: Excellent choice for producing high volume 3D thermoplastic foam, film and non-woven fabric with complex feature requirements
- Materials: Polyethylene Foams, EVA Foams, PVC Foams, PU Foams, Nonwoven Fabrics, TPU Films
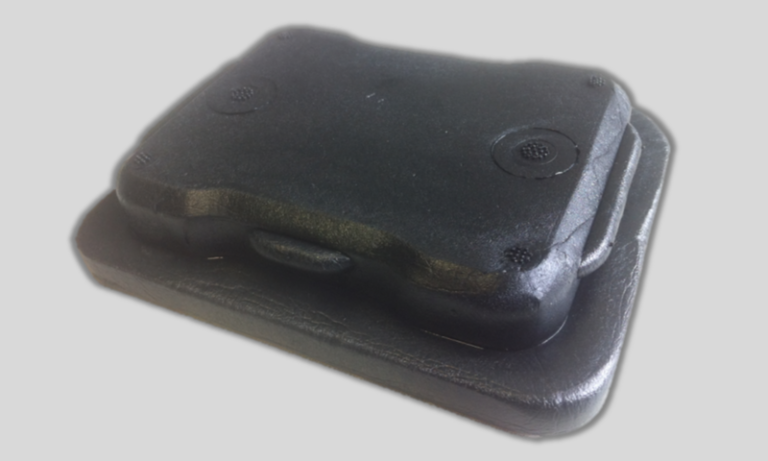
Vacuum Forming
Pre-heated material is drawn onto a tool contour via vacuum
- Features: Excellent choice to produce a uniform thin wall of 3D hollow parts of various materials in a short lead time
- Materials: Polyethylene Foams, EVA Foams, PVC Foams, Plastic Films
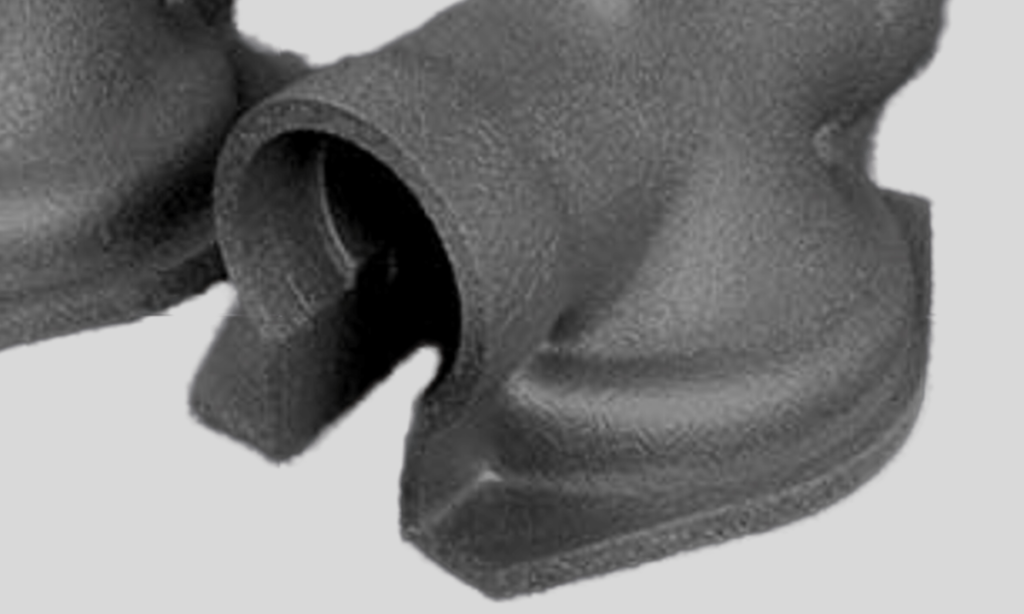
TwinSheet Forming
Two sheets of material are heated and formed simultaneously or sequentially and then pressed together
- Features: Excellent choice for products that requires 3D hollow foam parts with formed features on both ends without secondary bonding requirement
- Materials: Polyethylene Foams, EVA Foams, PVC Foams, Plastic Films
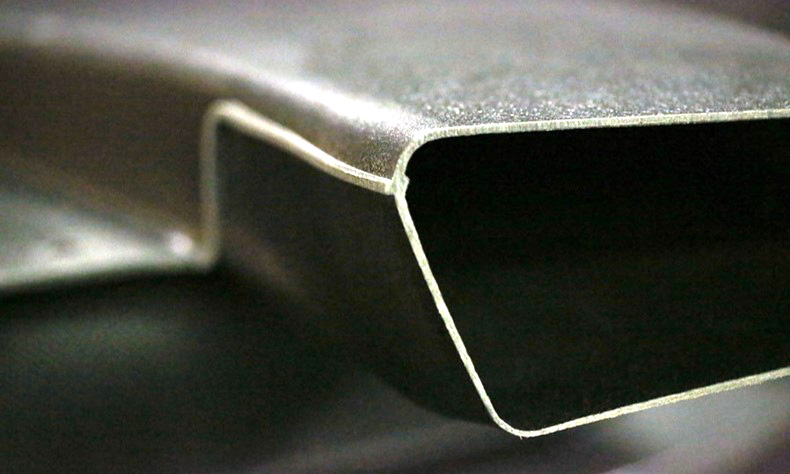
Applications
Depending on applications, the foam material selected can be thermoformed and shaped to meet the exact requirements.
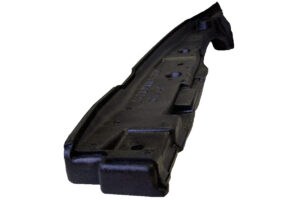
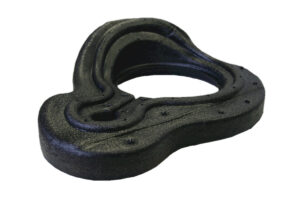
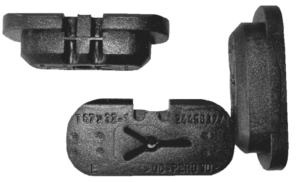
Heat Press Forming
Applications
- Seals, gaskets, product padding, liner pads, insulation parts, cushions
Requirements
- Lightweight, flexible, acoustic dampening, thermal insulation, vibration dampening, shock absorption
Materials
- PE foam, PP foam, EVA foam, Polyurethane foam
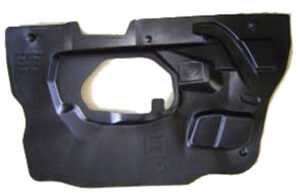
Vacuum Forming
Applications
- Seals, insulation sleeves, trays, containers
Requirements
- Lightweight, flexible, acoustic dampening, thermal insulation, vibration dampening, shock absorption
Materials
- PE foam, PP foam, EVA foam, PVC foam
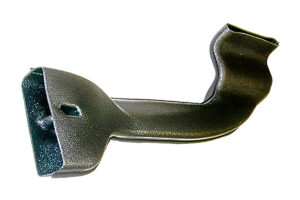
Twin-Sheet Thermoforming
Applications
- HVAC air duct
Requirements
- Lightweight, flexible, exceptional acoustic dampening, low thermal conductivity, no water condensation
Materials
- PE foam, PP foam